Unveiling the Magic of Carbon Trapping: A Shino Glaze Adventure
Hey everyone, Susan here, your friendly neighborhood ceramics enthusiast! Today, we’re diving into the fascinating world of carbon trapping, a technique that can produce stunning, one-of-a-kind surfaces on your ceramic pieces. If you’ve ever been captivated by those mesmerizing grey and black patterns reminiscent of a starry night sky, then get ready to unlock the secrets behind this captivating process.
What Exactly is Carbon Trapping?
Imagine this: you’re a potter, and your kiln is a magical cauldron. Inside, amidst the dancing flames, a transformation is taking place. Carbon, in the form of tiny soot particles, is being drawn to the surface of your glazed pottery. As the glaze melts, it acts like a protective embrace, trapping the carbon and creating those captivating patterns we all adore.
In essence, carbon trapping is the art of capturing soot within a glaze during the firing process. It’s a delicate dance between heat, atmosphere, and the glaze itself, resulting in truly unique and breathtaking finishes.
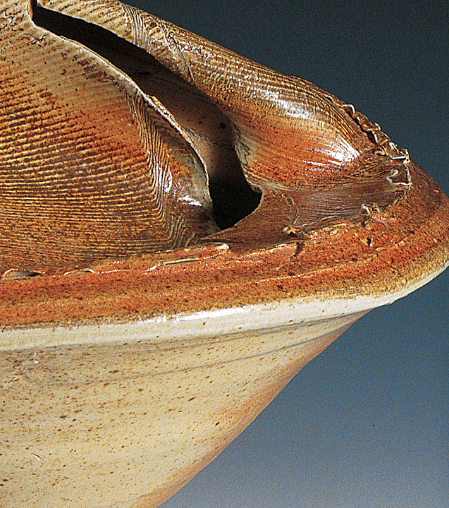
The Alchemy of Soot: Creating the Magic
So, how do we conjure this magical soot? It all starts with a fuel-fired kiln and a touch of controlled chaos. By limiting the air supply to the kiln, we create a smoky, oxygen-deprived environment – a process called reduction. This reduction atmosphere is crucial for producing the soot we need for carbon trapping.
Think of it like this: when you light a candle and the flame burns clean, that’s oxidation – plenty of oxygen. But when you restrict the oxygen, like when you blow out a candle, you get that smoky trail of soot. The same principle applies in our kiln!
Timing is Everything: The Dance Between Reduction and Oxidation
Now, here’s where the real artistry comes in. Timing is paramount in carbon trapping. We need to maintain this reduction atmosphere and allow soot to deposit on our pottery until the glaze reaches its melting point. If we switch to an oxidation atmosphere (reintroduce oxygen) too early, the soot will simply burn away, leaving us with nothing but disappointment.
Once the glaze melts and forms a protective seal over the surface, we can safely switch back to oxidation. The trapped carbon is locked in, forever immortalized beneath the glassy surface.
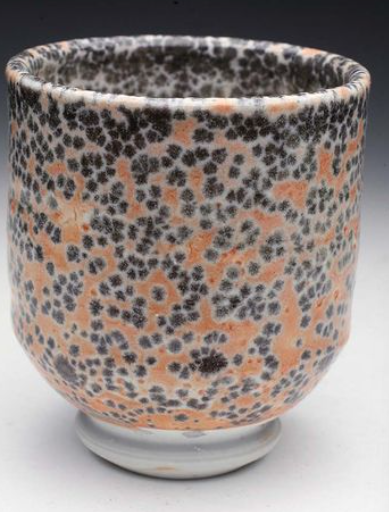
The Perfect Glaze: A Balancing Act
Not all glazes are created equal when it comes to carbon trapping. We need a glaze that can withstand the high temperatures of reduction firing while still being fluid enough to capture the soot.
Here’s what we look for in a carbon trapping glaze:
- High Alumina Content: Alumina, often derived from clay, adds viscosity to the glaze, preventing it from becoming too runny at high temperatures.
- Low Melting Point Fluxes: Fluxes like sodium and lithium help lower the glaze’s melting point, allowing it to flow and trap the carbon effectively.
Finding the perfect balance between these elements is key to achieving those stunning carbon trapped effects.
A Shino Glaze Recipe to Ignite Your Creativity
Ready to embark on your own carbon trapping adventure? Here’s a classic Shino glaze recipe, known for its beautiful carbon trapping capabilities:
Ingredients:
- Nepheline Syenite: 50%
- Grolleg Clay: 25%
- Silica: 25%
This recipe provides a good starting point. Remember, you can always experiment with different ratios and even add small amounts of colorants to create your own unique variations.
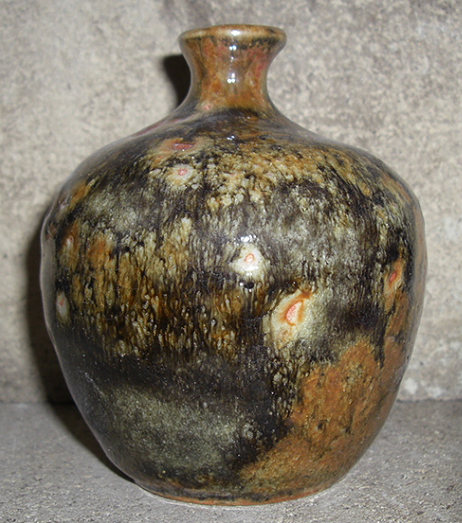
FAQs: Your Carbon Trapping Queries Answered
Q: Can I achieve carbon trapping in an electric kiln?
A: Unfortunately, no. Carbon trapping requires a fuel-fired kiln to create the necessary reduction atmosphere. Electric kilns maintain an oxidation environment, making carbon trapping impossible.
Q: What types of clay bodies work best for carbon trapping?
A: Porcelain and stoneware are excellent choices for carbon trapping due to their ability to withstand high temperatures.
Q: How can I tell when the glaze has melted enough to seal in the carbon?
A: This comes with experience and careful observation. Using pyrometric cones and understanding the visual cues of your glaze can help you determine the optimal time to switch back to oxidation.
Q: Where can I learn more about glaze chemistry and firing techniques?
A: Numerous resources are available online and in libraries. The websites of ceramic suppliers, pottery communities, and educational institutions often offer a wealth of information.
Remember, the journey of a potter is one of constant exploration and discovery. Embrace the unexpected, experiment with different techniques, and let your creativity flow!
Post Comment