Unlocking the Magic of Glaze: A Beginner’s Guide to Understanding Glaze Structure
Hey there, fellow ceramic enthusiasts! It’s Susan, your friendly neighborhood art aficionado, and today we’re diving deep into the mesmerizing world of glazes.
For many of us, the allure of ceramics lies in transforming ordinary clay into beautiful, functional art. And what better way to achieve that than with the magic of glaze? But understanding how glazes work can feel like deciphering an ancient language. Fear not, my friends! I’m here to break down the complexities of glaze structure into simple, digestible pieces.
Think of this as your beginner’s guide to unlocking the secrets behind those stunning, glossy finishes. We’ll explore the essential components of a glaze, uncover the roles they play, and even delve into the fascinating world of ceramic stains. By the end of this journey, you’ll be well on your way to creating your own unique glazes and adding that extra touch of magic to your ceramic creations.
Ready to get glazing? Let’s dive in!
What Exactly is Glaze Structure?
Imagine building a house. You wouldn’t just pile up bricks without a plan, right? You need a solid structure to hold everything together. Glaze works similarly. It’s not just a colorful coating; it’s a carefully balanced system of ingredients that interact during firing to create the desired surface effects.
Understanding this structure is key to predicting how a glaze will behave in the kiln and achieving consistent, beautiful results. It’s like having the blueprint to your dream ceramic finish!
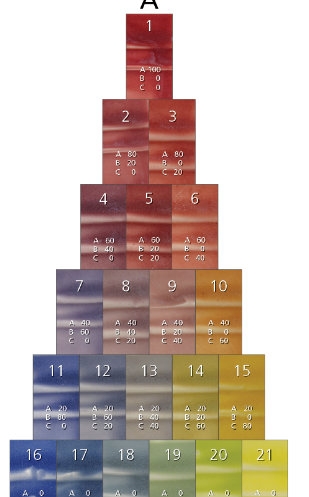
The Three Musketeers of Glaze: Glass Formers, Fluxes, and Refractories
Every glaze, no matter how simple or complex, relies on the interplay of three main components:
Glass Formers: These are the backbone of your glaze, providing the structural foundation for the glassy surface. Think of them as the bricks in our house analogy. Silica (SiO2), found in materials like quartz and flint, is the most common glass former.
Fluxes: Fluxes are the great melting mediators! They lower the melting point of the glass formers, allowing the glaze to mature and flow at achievable temperatures. Without fluxes, your glaze would remain a stubborn, powdery mess. Common fluxes include feldspar, whiting (calcium carbonate), and wood ash.
Refractories: These are the stubborn members of the glaze trio, resisting melting and adding durability to the final surface. They prevent the glaze from becoming too runny and help control its texture. Alumina (Al2O3), found in clay and feldspar, is a key refractory.
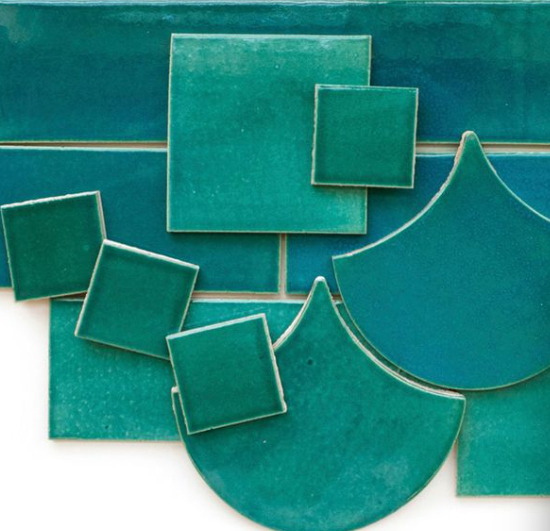
A Simple Analogy to Remember it All
John Britt, a renowned ceramic artist, uses a brilliant analogy to explain how these components work together. He compares the glaze structure to a group of friends:
- The glass former is like the shy friend who prefers to stay put.
- The flux is the social butterfly, encouraging everyone to loosen up and mingle.
- The refractory is the responsible one, making sure things don’t get too out of hand.
Just like in a well-balanced friend group, the key to a successful glaze lies in finding the perfect harmony between these three components.
The Colorful World of Ceramic Stains
Now, let’s add some color to our glaze conversation! While the basic glaze structure provides the foundation, ceramic stains are the artistic tools that allow us to paint our ceramic canvases with vibrant hues.
What are Ceramic Stains?
Stains are essentially pre-melted mixtures of coloring oxides and other ceramic materials. They offer a consistent and reliable way to achieve specific colors in your glazes.
Why Use Stains?
- Consistency: Stains provide predictable and repeatable color results, unlike raw oxides that can be more volatile.
- Safety: Many raw oxides are toxic, but stains are formulated to be safer to handle and use.
- Versatility: Stains come in a vast spectrum of colors, opening up endless creative possibilities.
Exploring Different Types of Stains:
- Traditional Stains: These are the workhorses of the ceramic color world, offering a wide range of hues for various firing temperatures and atmospheres.
- Encapsulated Stains: These specialized stains encapsulate the coloring agents within a zircon matrix, resulting in incredibly vibrant and stable colors, even at high temperatures.
Tips for Using Stains:
- Start Small: A little stain goes a long way! Begin with small additions (around 1-8%) and gradually increase until you achieve the desired intensity.
- Test, Test, Test: Always test your stains in small batches before committing to a full piece. Firing temperature and glaze base can significantly impact the final color.
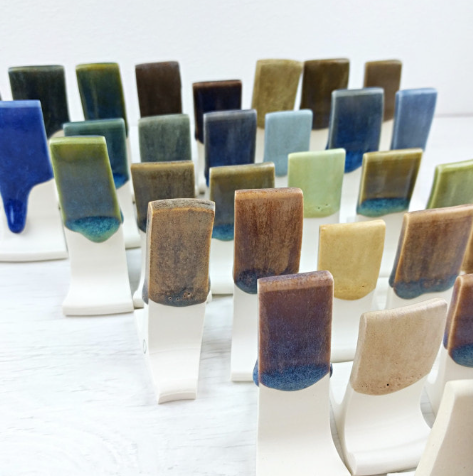
Resources for Further Exploration
Ready to delve deeper into the world of glazes and stains? Here are some excellent resources to guide your journey:
- Digitalfire: This comprehensive online database offers a wealth of information on glaze chemistry, materials, and firing. (https://digitalfire.com/)
- Ceramic Arts Network: This website is a treasure trove of articles, videos, and resources for ceramic artists of all levels. (https://ceramicartsnetwork.org/)
- John Britt Pottery: Explore the work and insights of John Britt, the master of glaze analogies! (https://johnbrittpottery.com/)
Embracing the Journey of Glaze Discovery
Remember, mastering the art of glaze takes time, experimentation, and a healthy dose of curiosity. Embrace the journey, don’t be afraid to make mistakes, and most importantly, have fun exploring the endless possibilities of this captivating ceramic element!
Happy glazing, everyone!
Post Comment