The Allure of Fire: Exploring Different Types of Fuel-Burning Kilns
For centuries, the transformative power of fire has been essential to the ceramic arts. Long before the advent of electric kilns, artists relied on the raw energy of fuel-burning kilns to bring their creations to life. While modern technology offers convenience, there’s a captivating magic to fuel-fired pottery – a unique aesthetic unattainable through other means. This exploration delves into the world of fuel-burning kilns, uncovering the distinct characteristics and artistic possibilities of each type.
Understanding the Basics: Fuel Types and Kiln Designs
Fuel-burning kilns, as the name suggests, utilize combustible materials to generate heat. These fuels can be broadly categorized into three types:
- Solid Fuels: Historically, materials like wood, coal, and even animal dung served as fuel sources. Today, wood remains the most prevalent solid fuel in the ceramic world, particularly for high-fire applications.
- Liquid Fuels: Oil, and kerosene offer a convenient alternative to solid fuels, providing consistent heat and eliminating the need for constant stoking.
- Gaseous Fuels: Natural gas and propane are popular choices for their clean-burning properties and ease of control. They are readily available in many areas and produce minimal ash residue.
The design of a fuel-burning kiln significantly influences the path of heat and the resulting effects on the pottery. Three primary designs dominate the field:
Updraft Kilns: These kilns feature a firebox at the base, with flames traveling upwards through the ware chamber and exiting through a chimney at the top. Updraft kilns are often used for low-fire applications.
Crossdraft Kilns: In this design, the firebox sits on one side of the kiln, and the flue (exhaust) is located on the opposite side. Heat travels horizontally across the ware chamber before being drawn upwards through the chimney. This design promotes more even heat distribution compared to updraft kilns.
Downdraft Kilns: Considered the most efficient design, downdraft kilns direct the flame upwards from a firebox and then downwards through the ware chamber. The exhaust gases then travel through an underfloor chamber before exiting through the chimney. This design maximizes heat circulation and allows for higher firing temperatures, making it suitable for stoneware and porcelain.
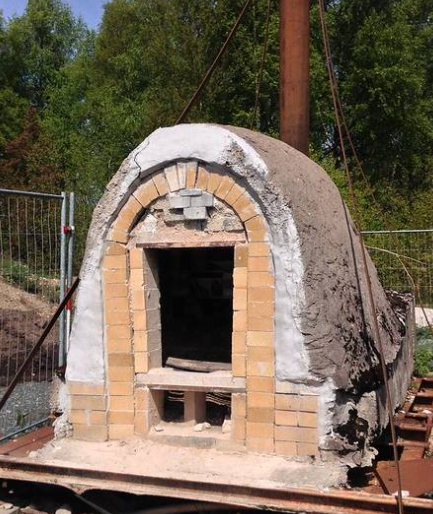
A Closer Look at Specific Fuel-Burning Kilns
Each type of fuel-burning kiln brings its own personality to the ceramic process, influencing the final appearance and character of the fired pieces.
1. The Wood Kiln: Embracing the Dance of Flame and Ash
Wood-fired pottery holds a special place in the ceramic world, revered for its unique aesthetic and organic beauty. The long firing cycles, often lasting several days, create an intimate connection between the artist, the kiln, and the fire.
Wood kilns, primarily utilizing downdraft or crossdraft designs, produce captivating effects:
Ash Glazes: As wood burns, it releases fine ash particles that settle on the pottery’s surface. At high temperatures, these ashes melt, creating a natural glaze with subtle variations in color and texture. The unpredictable nature of ash deposits results in one-of-a-kind pieces with a sense of depth and history.
Flashing: The fluctuating atmosphere within a wood kiln, characterized by varying oxygen levels, can cause unique color reactions in both clay and glazes. Iron oxide, a common component in many glazes, responds dramatically to these atmospheric changes, producing a range of warm reds, oranges, and browns.
Reduction Effects: Wood firing often creates a reducing atmosphere, where there is a limited supply of oxygen within the kiln. This reduction process can enhance certain colors and create unique surface effects. For example, copper oxide, typically producing green in an oxidizing atmosphere, transforms into vibrant reds and lustres in a reducing environment.
2. Oil and Gas Kilns: Precision and Versatility
Oil and gas kilns offer greater control and predictability compared to wood firing, making them a popular choice for both studio and production potters.
Oil Kilns: Often favored for their ability to achieve high temperatures and create a slightly more reduced atmosphere than gas kilns, oil kilns produce rich colors and subtle variations in glaze textures.
Gas Kilns: Known for their clean-burning properties and ease of use, gas kilns are particularly well-suited for urban studios or areas where wood firing may not be feasible. They offer precise temperature control and consistent results.
3. Salt and Soda Kilns: The Magic of Vapor Glazing
Salt and soda kilns utilize a fascinating process where vaporized sodium creates a unique glaze on the surface of the pottery.
Salt Kilns: During a salt firing, sodium chloride (common table salt) is introduced into the kiln at high temperatures. The salt vaporizes and reacts with the silica and alumina in the clay body, forming a sodium silicate glaze. Salt glazes are known for their characteristic “orange peel” texture and a range of colors from warm tans to deep browns.
Soda Kilns: Similar to salt firing, soda firing introduces sodium carbonate into the kiln atmosphere. Soda firing produces a slightly thinner glaze than salt firing and tends to enhance the colors of applied glazes, creating vibrant and often unpredictable results.
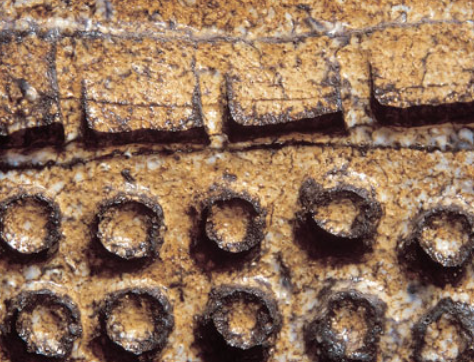
Exploring the World of Fuel-Burning Kilns
Fuel-burning kilns offer a captivating blend of art and science, allowing ceramic artists to harness the power of fire to transform raw materials into stunning works of art. From the unpredictable beauty of wood firing to the precision of gas kilns and the unique effects of salt and soda, each type of kiln presents its own set of possibilities and challenges.
For those drawn to the allure of flame and the magic of transformation, exploring the world of fuel-burning kilns is an enriching and rewarding journey.
Further Exploration:
- The Art of Wood Firing: Delve deeper into the intricacies of wood firing and the factors that influence the final results.
- Salt and Soda Firing: A Comparison: Explore the similarities and differences between salt and soda firing techniques.
- Building Your Own Kiln: For the adventurous ceramic artist, consider the rewarding experience of building your own fuel-burning kiln.
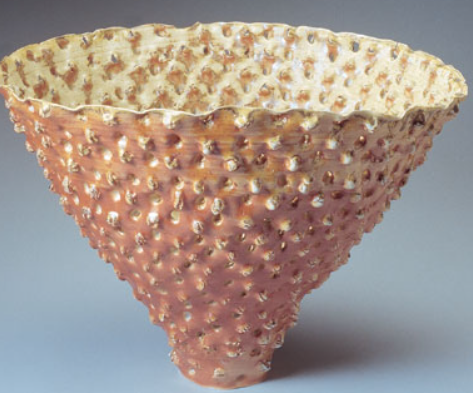
Post Comment