Mastering the Art of Slip Casting: From Mixing to Mold Mastery
Hey everyone, it’s Susan, your resident craft enthusiast, back with another deep dive into the fascinating world of ceramics! Today, we’re tackling a technique that opens up a world of creative possibilities: slip casting. Whether you’re dreaming of replicating intricate sculptures or crafting a set of perfectly uniform mugs, understanding slip casting can truly elevate your ceramic game.
Now, I know what you might be thinking: “Slip casting? Sounds complicated!” And trust me, I’ve been there. But fear not, my fellow creatives, because I’m here to break down the process into manageable steps, sprinkled with tips and tricks I’ve gathered along the way. Let’s dive in!
What Exactly is Slip Casting?
In the simplest terms, slip casting is like creating a ceramic clone. Imagine pouring liquid clay – called “slip” – into a plaster mold. The plaster absorbs the water from the slip, leaving behind a solid layer of clay in the shape of the mold. Once dry, you have a ceramic replica! Pretty cool, right?
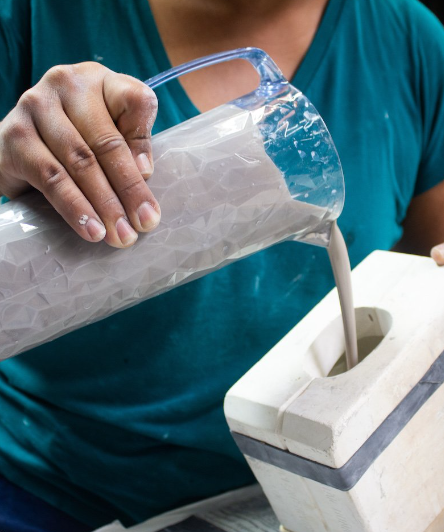
The Magic Starts with the Slip: Mixing It Right
The foundation of successful slip casting lies in the slip itself. It needs to be the perfect consistency: not too thick, not too thin, but just right, like Goldilocks’ porridge! Here’s a breakdown of how to mix a batch of casting slip, using a recipe from the University of the Arts:
Ingredients:
- Water: 5000 grams
- Darvan #7 (deflocculant): 40 grams (0.4% of total dry weight)
- Bentonite (for plasticity): 50 grams (0.5% of total dry weight, can increase to 1%)
- Grolleg (English Kaolin): 5500 grams
- Nepheline Syenite (flux): 2300 grams
- Flint (Silica): 2200 grams
Step-by-Step Mixing Guide:
- Blunge: In a sturdy bucket, combine the water and Darvan using a heavy-duty drill equipped with a mixing attachment (a squirrel-cage or jiffy mixer works wonders!). Slowly add the bentonite while mixing, ensuring it’s thoroughly incorporated.
- Add Dry Ingredients: Gradually introduce the dry materials – Grolleg, Nepheline Syenite, and Flint – while continuously mixing. This prevents clumping and ensures a smooth, consistent slip.
- Adjust Consistency: Once all the dry ingredients are mixed in, you might need to fine-tune the consistency.
- Too thick? Add small amounts of water, a few drops at a time, mixing thoroughly between each addition.
- Too thin? Add a touch more Darvan (up to 0.2% of the total weight, but no more than 0.6% overall).
- Rest and Re-Mix: Allow the slip to rest overnight. This gives the ingredients ample time to hydrate fully. The next day, give it another good mix.
- Check Specific Gravity: Before you start casting, it’s crucial to check the slip’s specific gravity. This measures its density compared to water. Ideally, you’re aiming for a specific gravity between 1.7 and 1.8. You can find specific gravity hydrometers at most ceramic supply stores.
Pro Tip: While you can use the slip immediately after mixing, allowing it to rest overnight yields a smoother, more consistent casting slip.
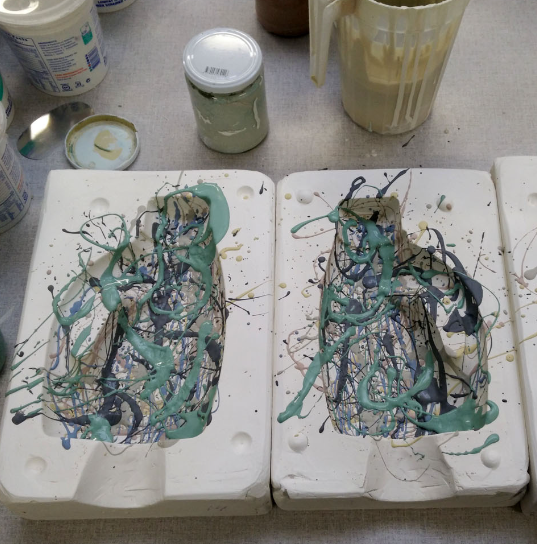
Mold Mastery: Creating and Caring for Your Casting Molds
Now that you’ve got your slip ready, let’s talk about molds. These are the vessels that will bring your ceramic visions to life!
Types of Molds:
- One-Piece Molds: Ideal for simple shapes, these molds have a single cavity and are open at the top.
- Two-Piece Molds: Used for more complex forms, these molds consist of two halves that fit together, creating an internal cavity for casting.
Essential Mold Maintenance Tips:
- Smooth Operator: After creating your plaster molds, smooth the edges with a surform tool. This prevents plaster bits from breaking off and contaminating your slip.
- Vinegar Wash: Regularly wipe down your molds with a solution of equal parts water and vinegar. This helps remove any residual mold soap and keeps the plaster clean.
- Sanding for Success: Lightly sand your molds with fine-grit wet/dry sandpaper (at least 600 grit). This creates a smoother surface, reducing the chance of air bubbles and making it easier to release your cast pieces.
Troubleshooting Mold Issues:
- The “Fuzzy Beard” Dilemma: If you notice a white, fuzzy buildup on your molds, it’s a sign they’re getting old and worn out. This “beard” is often caused by sodium silicate in the slip reacting with the plaster. While a vinegar wash can help, it might be time to retire those molds and make fresh ones.
- Extending Mold Life: Using Darvan as a deflocculant, instead of sodium silicate, can help prolong the life of your molds. While a bit pricier, Darvan is gentler on plaster.
Boosting Efficiency with Gang Molds:
For those looking to streamline production, gang molds are a game-changer! These multi-cavity molds allow you to cast multiple pieces simultaneously, saving time and ensuring consistency.
Creating a Gang Mold:
- Prepare your plaster mold as you usually would for a single object mold.
- Instead of placing one object on the clay bed, arrange several, ensuring at least an inch of space between each to allow for adequate plaster thickness.
- Proceed with creating the mold as you would for a single object mold.
3 Pro Tips for Slip Casting Success:
- Mind the Bubbles: Air bubbles are the nemesis of smooth, flawless casts. To minimize them:
- Mix your slip slowly and thoroughly.
- Tap the sides of your mold gently after pouring to release any trapped air.
- Consider using a vacuum chamber to remove bubbles from the slip before casting.
- Perfect Timing is Key: The time you leave the slip in the mold determines the thickness of your cast piece. Experiment with different drying times to achieve the desired wall thickness.
- Release with Care: Once your piece has dried sufficiently, it’s time to demold. Gently tap the mold to loosen the cast piece and carefully ease it out.
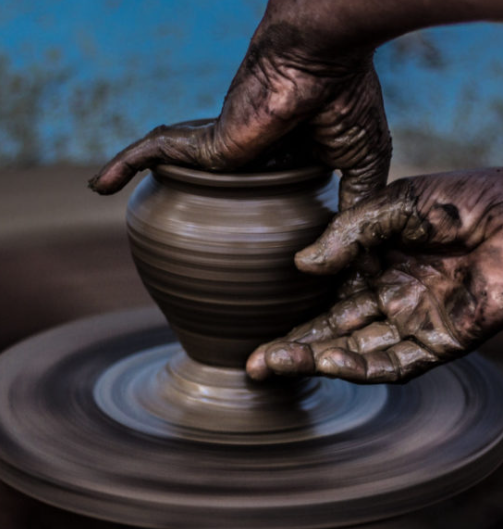
Resources for Further Exploration:
- Ceramic Arts Network: https://ceramicartsnetwork.org/ – A treasure trove of articles, videos, and resources for ceramic artists of all levels.
- The Ceramic School: https://theceramicschool.com/ – Offers a wide range of online courses and workshops on various ceramic techniques, including slip casting.
- Digitalfire: https://digitalfire.com/ – An invaluable resource for understanding ceramic materials, glazes, and firing processes.
Embrace the Joy of Slip Casting!
I hope this deep dive into slip casting has ignited your creative spark! It’s a truly rewarding technique that allows you to explore intricate designs and create multiples of your ceramic masterpieces. Remember, practice makes perfect, so don’t be afraid to experiment, embrace the happy accidents, and most importantly, have fun!
Happy casting, everyone!
Post Comment