Banishing Glaze Faults: Mastering the Art of Bisque Firing
Hey there, fellow clay enthusiasts! It’s Susan, your go-to gal for all things handicraft, and today we’re diving deep into the fascinating world of ceramics with a focus on a crucial step: bisque firing.
Have you ever pulled a piece out of the kiln, only to be met with frustrating glaze defects? Don’t worry, we’ve all been there! While it’s easy to blame the glaze itself, the culprit often lies in a frequently overlooked stage – the bisque firing.
A successful glaze firing hinges on a well-executed bisque firing. It’s during this initial firing that we lay the groundwork for flawless glaze application and stunning final results. So, let’s unravel the mysteries of bisque firing and banish those pesky glaze faults for good!
Understanding the Enemy: Common Glaze Faults and Their Root Cause
Before we delve into the solution, let’s take a closer look at the common glaze faults that plague us ceramic artists:
- Bloating: Those unsightly bubbles and blisters on the surface of your pottery are a clear sign of bloating.
- Black Coring: A dark, often discolored center within your ceramic piece indicates incomplete carbon burnout.
- Pinholing: Tiny holes dotting the surface of your glaze are not only aesthetically displeasing but can also compromise the piece’s structural integrity.
- Blistering: Similar to bloating, blistering appears as raised bumps on the glaze surface, often caused by trapped gases.
- Poor Color Development: Dull, muted, or uneven glaze colors can be incredibly frustrating, especially when you’ve envisioned vibrant hues.
Surprisingly, the root cause of these seemingly unrelated glaze faults often lies in the incomplete removal of carbon and sulfur during the bisque firing.
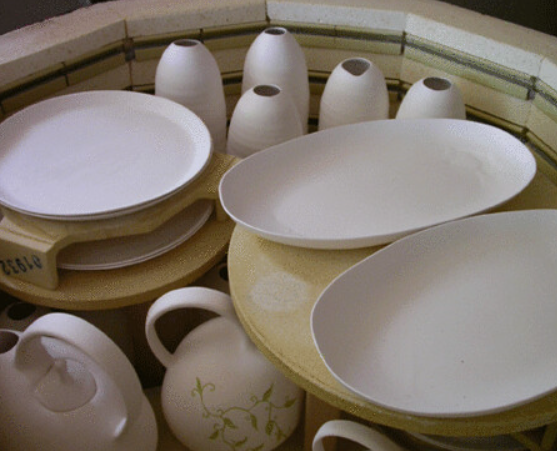
The Science Behind the Solution: Carbon, Sulfur, and the Importance of Oxidation
Many materials we use in ceramics, including clay itself, contain carbon and sulfur. These elements, while naturally occurring, can wreak havoc on our glazes if not properly eliminated during the bisque firing.
Think of it like this: imagine trying to paint a masterpiece on a canvas covered in dust and debris. The result? A muddled mess! Similarly, carbon and sulfur act as barriers, preventing the glaze from properly adhering to the ceramic surface and leading to those dreaded defects.
The key to success? Oxidation!
Oxidation is a chemical process that occurs when carbon and sulfur react with oxygen in the kiln’s atmosphere. This reaction transforms these troublesome elements into gases, allowing them to escape the clay body, leaving behind a pristine surface primed for glazing.
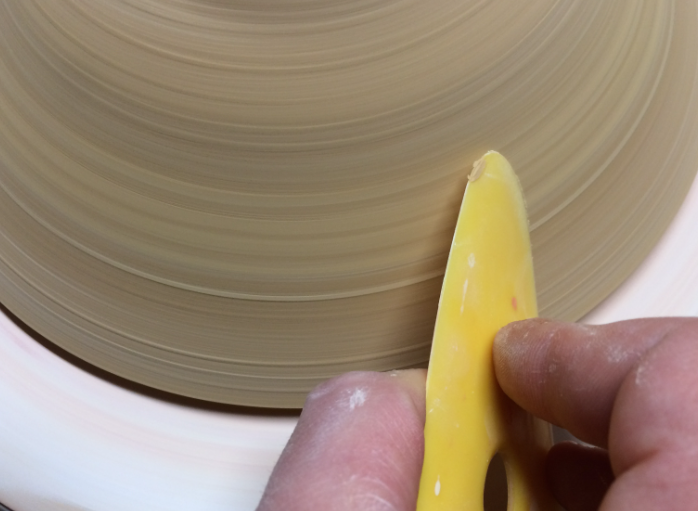
The Three Pillars of Complete Oxidation: Oxygen, Time, and Temperature
Achieving complete oxidation during bisque firing requires a delicate balance of three crucial factors:
Oxygen: Just like we need oxygen to breathe, the chemical reaction that eliminates carbon and sulfur requires a steady supply of oxygen within the kiln chamber. Without sufficient oxygen, the oxidation process is hindered, leading to incomplete burnout and, ultimately, glaze defects.
Time: Rushing the bisque firing is a recipe for disaster. Adequate time is crucial to allow oxygen to penetrate the clay body and react with the carbon and sulfur. Thicker pieces, densely packed kilns, and clay bodies with higher iron content require longer firing times to ensure complete oxidation.
Temperature: Different types of carbon burn off at different temperatures. Organic carbon, found in materials like binders and additives, burns off at lower temperatures, while inorganic carbon, present in clay and other ceramic materials, requires higher temperatures for complete elimination.
A Bisque Firing Schedule for Success: Your Roadmap to Flawless Glazes
Now that we understand the science behind bisque firing, let’s translate that knowledge into a practical firing schedule. Keep in mind that this is a general guideline, and you may need to adjust it based on your specific kiln, clay body, and desired results.
Electric Kiln Bisque Firing Schedule:
Segment | Rate (°F/hour) | Temperature (°F) | Hold (hours) |
---|---|---|---|
1 | 150-200 | 200 | 1 |
2 | 200 | 400 | 1 |
3 | 200 | 600 | 1 |
4 | 150-200 | 1000 | 1 |
5 | 100-150 | 1650-1700 | 1-2 |
6 | Cool to room temperature |
Let’s break down this schedule:
- Segments 1-3: These initial segments focus on slowly driving off moisture from the clay body. Gradual heating prevents cracking and warping, ensuring your pieces remain intact.
- Segment 4: This is where the magic of oxidation begins! We ramp up the temperature to encourage the reaction between oxygen and carbon.
- Segment 5: We reach the crucial temperature range for inorganic carbon and sulfur burnout. The slower heating rate and hold time allow ample opportunity for complete oxidation.
- Segment 6: Patience is key! Allowing the kiln to cool slowly prevents thermal shock and ensures your bisque ware is ready for glazing.
Pro Tip: For manual kilns, apply these same principles by gradually increasing the temperature and ensuring adequate ventilation throughout the firing process.
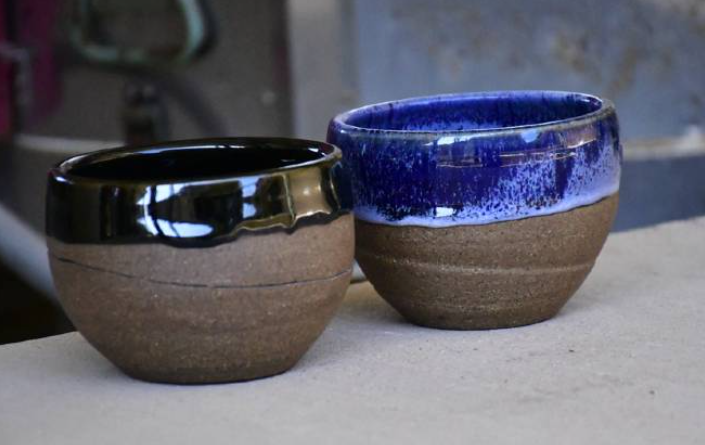
Beyond the Basics: Additional Tips for Bisque Firing Success
- Kiln Wash: Always apply kiln wash to your kiln shelves to prevent glazed pieces from sticking during firing.
- Kiln Venting: Proper ventilation is crucial for supplying oxygen and removing harmful gases. Ensure your kiln is properly vented throughout the firing process.
- Cone Packs: Use cone packs to accurately monitor the kiln’s temperature and ensure you’re reaching the desired heat work.
- Experimentation: Don’t be afraid to experiment and fine-tune your bisque firing schedule based on your specific needs and observations. Keep a firing log to track your adjustments and results.
Remember: A well-executed bisque firing is an investment in the success of your glazed pottery. By understanding the science behind oxidation and implementing a carefully crafted firing schedule, you can banish glaze faults and unlock the full potential of your ceramic creations!
Happy potting!
Further Exploration:
- The Spruce Crafts: Bisque Firing: A comprehensive guide to bisque firing, covering everything from the basics to troubleshooting tips.
- Ceramic Arts Network: Understanding Atmospheric Firing: Delve deeper into the role of atmosphere in ceramic firing, including oxidation and reduction.
- Digitalfire: Carbon in Clay Bodies: Explore the impact of carbon on clay bodies and the importance of proper burnout.
Post Comment